1、 Product performance and features:
Hot melt welding (exothermic fusion welding) is a welding method that uses the chemical reaction of exothermic flux as a heat source to generate high temperature and achieve the welding purpose through the investment mold. It does not require external energy and is the best method for welding metal conductors. The ability to completely fuse copper and copper, copper and steel, and other similar or different metals, achieving true molecular bonding, thus making the lightning protection grounding device a permanent maintenance free device.
2、 Advantages of exothermic welding:
1. The current carrying capacity (melting point) of the fusion point is the same as that of the conductor, and it has good conductivity. After testing, the rate of change in the DC resistance ratio before and after welding is close to zero. This is incomparable to any traditional connection method.
2. Welding points are molecular bonds, permanent, and do not age.
3. Welding points are not affected by corrosion like copper.
4. Will not be damaged by high surge currents. Experiments have shown that under short-term high current impact, conductors melt before fusion welded joints.
5. Easy to operate and simple. No need for professional personnel.
6. The equipment is simple, lightweight, easy to carry, and easy to operate.
3、 Molten and auxiliary tools
1. Investment mold: The exothermic welding mold is made of graphite material, with fine workmanship and unique design, ensuring high performance and long service life. The design of the mold ensures that the melted solder can flow freely inside the cavity and can easily separate the mold from the welded connection point, thereby increasing the lifespan of the mold‘ The average welding time of the 'Leisdun' hot welding mold is over 80 times. If the welding points are simple and the operation is careful, it can be used over 100 times. We can equip various types of mold clamps that are easy to operate according to the needs of customers and on-site welding. The mold clamp is used to open and close the mold, and 'Leisdun' company has specialized mold clamps that correspond to the mold.
2. Auxiliary tools:
During the exothermic welding process, the following auxiliary tools are available:
Spray gun: used for dehumidification and preheating of the investment mold to enhance welding quality;
Mold clamp: After the fusion mold is aligned, use a mold clamp to clamp and fix the mold for smooth welding;
Horse bow: plays an auxiliary fixing role;
High temperature gloves: prevent hand burns;
Ignite gun: ignite welding powder;
Copper brush: remove impurities from the mold cavity;
Brush: Used for special anti-corrosion treatment of welded joints;
Fireproof mud: When the mold is worn or the gap is too large, fireproof mud can be used to seal it;
Toolbox: used to store welding tools for easy management of tool storage;
Screwdriver: plays an auxiliary role in operation.
4、 Common product specifications
5、 Application scope
1. Lightning protection grounding and surge protection.
2. Grounding engineering treatment for electrical equipment.
3. Petrochemical engineering construction.
4. Construction of photovoltaics, railways, highways, and airports.
5. Construction of intelligent buildings.
6. Cathodic anti-corrosion protection.
6、 Operating procedures
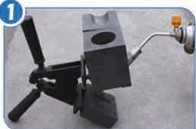
Clean the conductor and investment mold (if damp, it must be dried), place the conductor under the mold and conduct a contact test.
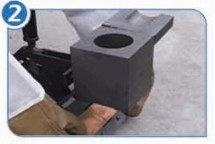
Place the two conductors to be welded into the fusion mold and align them in their respective positions.
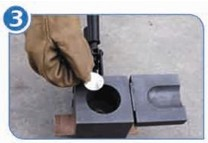
Clamp the investment mold, place the metal isolation plate, seal the flow port, and prevent the pre reaction welding agent from flowing into the mold cavity.
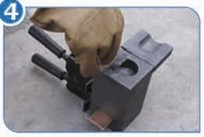
Pour the exothermic flux into the furnace, sprinkle some initial ignition powder at the mold mouth, and cover the top cover of the mold.
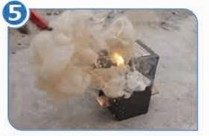
Ignite the ignition powder with an ignition gun, and the welding agent undergoes a safe exothermic reaction in the mold.
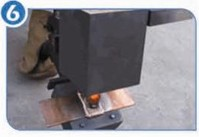
After the hot melt reaction is completed, the mold can be opened within 10-20 seconds. Use tools to remove the conductor and remove the slag.
七、焊接示意圖:
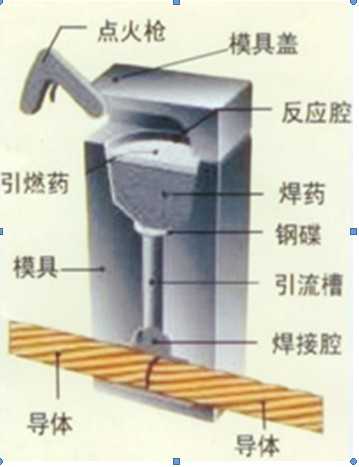
八、焊接好的成品:
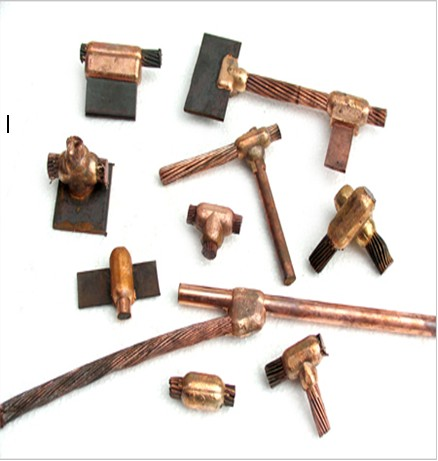
We can customize molds of different specifications and models according to user needs to achieve their ideal.
9、 Precautions for use
1. Before construction operation, it is necessary to ensure that the welded parts are free of dirt, and that there are no welding slag blocks or powder left in the fusion mold cavity and mold cavity from the previous welding.
2. Before construction operations, it is necessary to use a spray torch (or gas blowtorch) to dry the welded parts and investment molds to make them as free of moisture as possible.
3. During construction operations, before ignition, it is necessary to ensure that the fusion mold cover is closed and there are no gaps at the fusion mold closure.
4. During construction operations, before ignition, it is necessary to ensure that the welding point of the welded part is located at the center of the cavity.
5. During construction operations, no unrelated personnel are allowed to stay within a range of 1.50 meters on site.
6. During construction operations, flammable materials must not be placed within 1-2 meters of the site.
7. Operators must wear work gloves with a certain insulation effect.
8. Operators are not allowed to face the opening of the investment mold during construction.
9. When igniting, once the ignition powder is ignited, the operator must immediately leave the mold at least 1.50 meters away.
10. After the exothermic flux reaction is complete, no one is allowed to directly contact the investment mold and the welded parts.
11. After the exothermic flux reaction is complete, the investment mold and the welded part should be allowed to cool naturally for 10-20 seconds, and then removed from the investment mold using pliers (or similar tools).
12. Insulation treatment must be carried out on the welded parts only after the wires have completely cooled down.